Our Products
Our product development was driven by extensive consumer research and we now have a range of black opaque tights in 40, 60 and 100 denier in petite, standard and tall fittings.
They are seamless for a smooth, comfortable contour during wear and there are no sew in labels. Product information, washing instructions and bespoke branding are knitted into the waistband.
Our tights don’t streak or fade and don’t lose colour during washing.This is because colour is part of the DNA of the yarn and not added after the knitting process which has been the industry standard. We use a super microfibre yarn with LYCRA® which gives density of colour, great fit and super softness during wear.
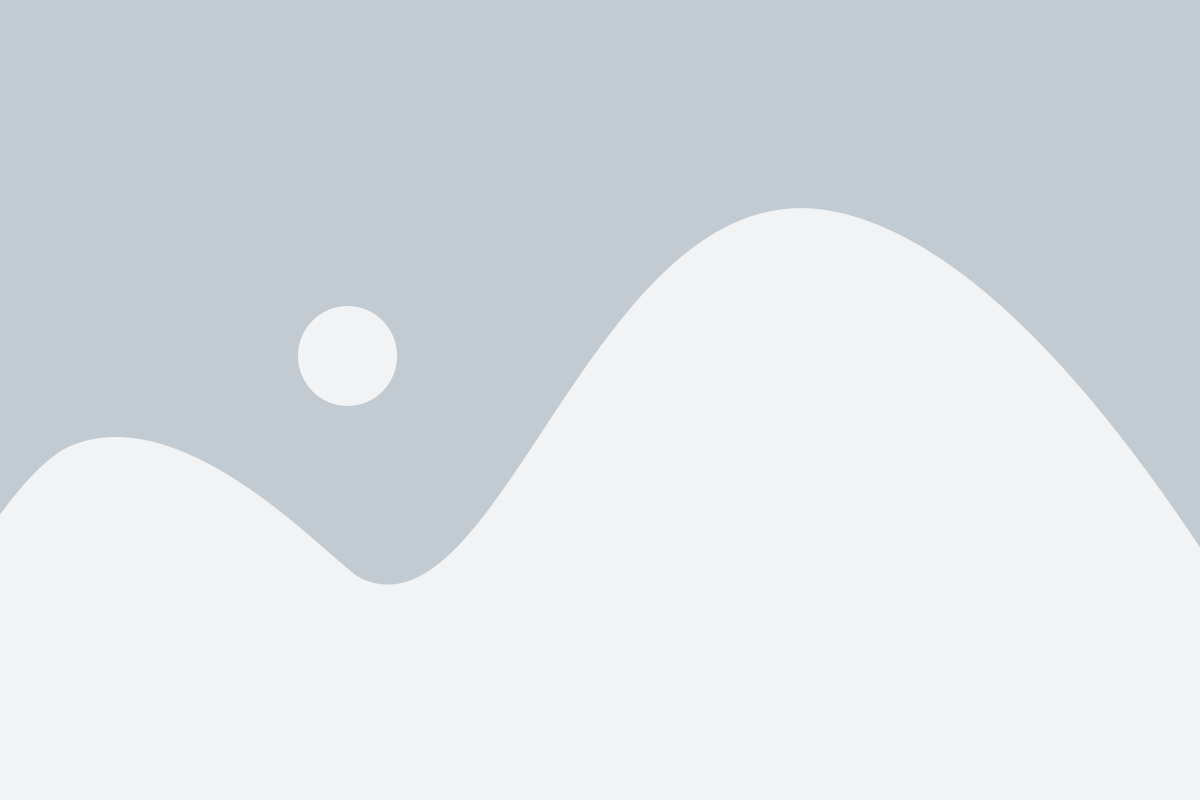
Read More
"They felt super snug yet had plenty of stretch for easy movement. I expected some sagging around the ankles (since this happens even in a small size) but in fact there was a good balance in body length to overall width and sizing. I’m looking forward to wearing them more!"
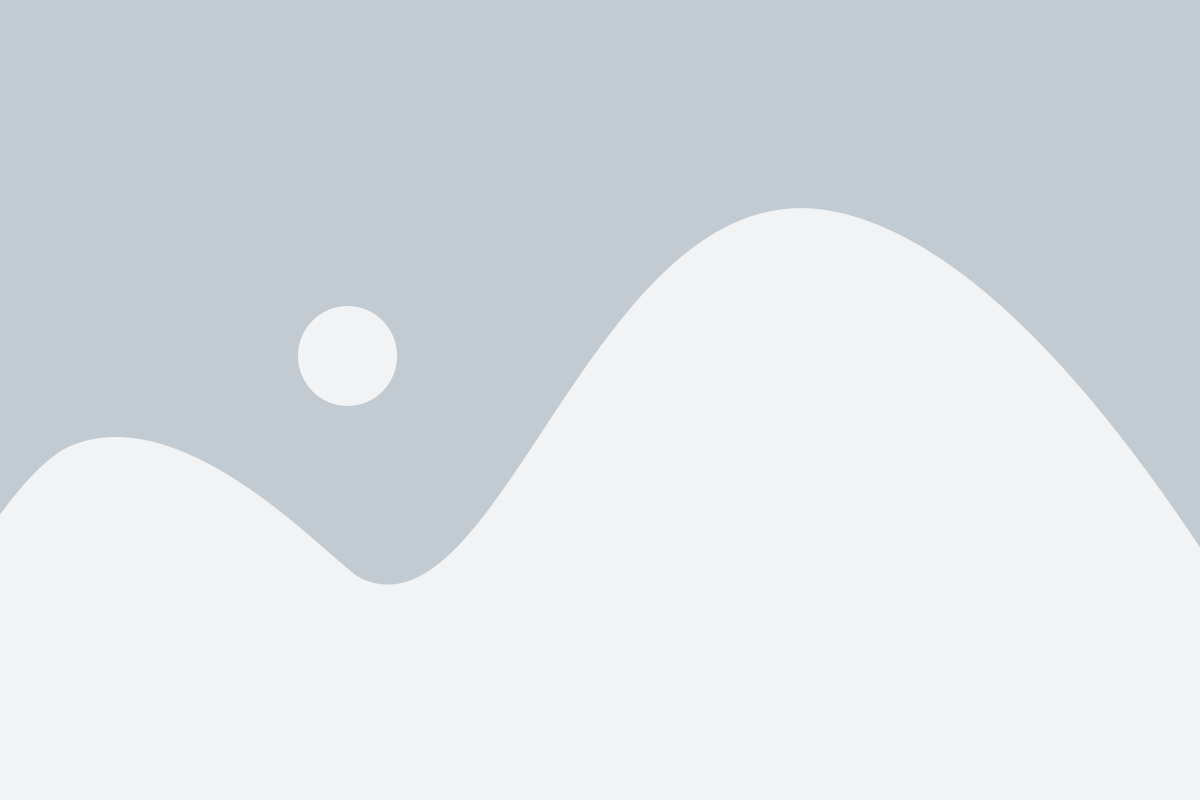
Read More
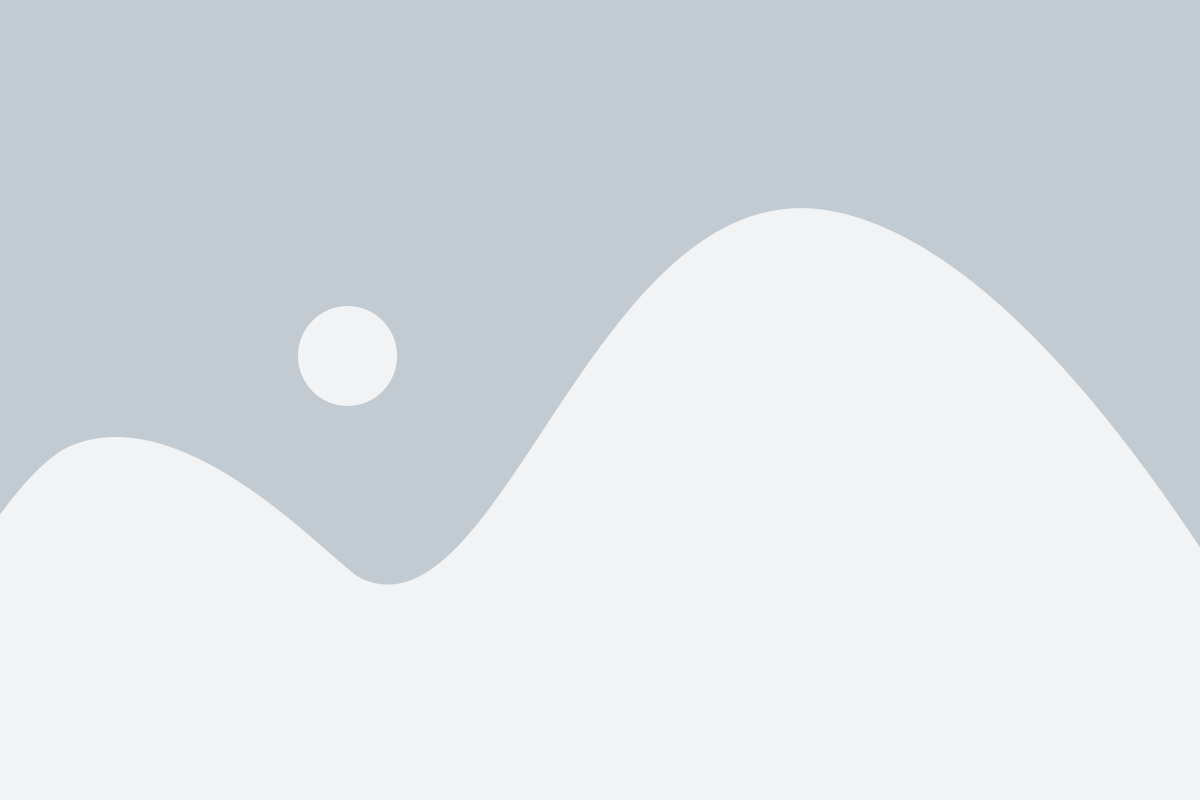
Read More
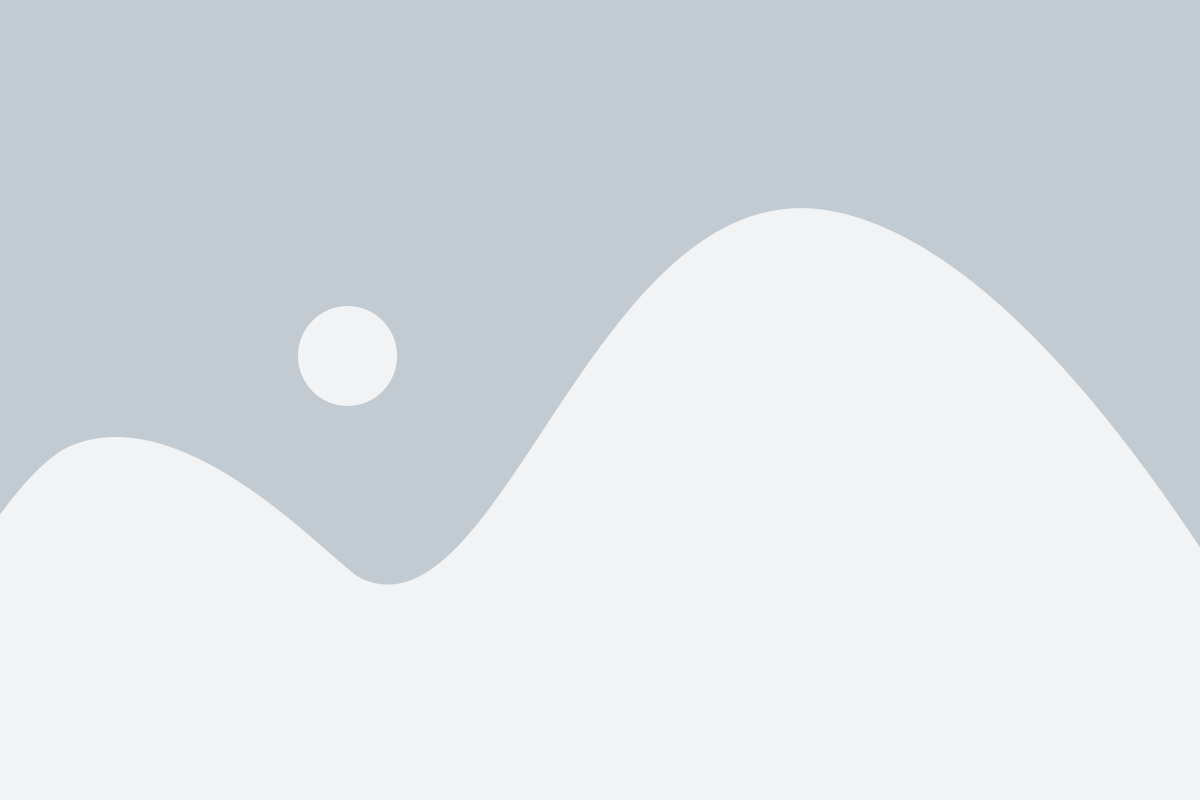
Read More
"I absolutely loved the lack of waistband, that felt really comfortable and is the bit I like least about normal tights. I am a regular size, but I usually end up snipping the waistband because I find it so uncomfortable."
Previous
Next